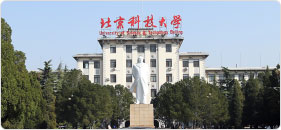
当前位置:首页 > 科学研究 > 科研动态
面向指标优化的高炉布料过程建模与控制
改革开放40年,我国的钢铁年产量从3178万吨跃升至8亿吨,中国钢产量占到世界钢产量的50%左右,完成了难以解读的天方夜谭式的巨变!如果没有这么多钢,靠进口钢材怎么能建成现在的中国,我们看到那么多高楼大厦,铁路,桥梁,似乎没去想是用钢铁堆起来的。
作为我国国民经济支柱的钢铁工业,也是高耗能和高排放产业,其中高炉炼铁能耗和排放占其主要部分。作为钢铁工业的排头兵的高炉炼铁过程,其高炉从40年前的1280立方米已经发展到拥有近20座4000立方米以上的高炉,5500立方米以上的高炉也有10座之多。高炉炼铁的原料入炉布料过程是影响高炉指标优化最关键的环节,具有运行机理复杂、环境恶劣、关键参量检测、指标优化和控制困难的特点。长期以来,高炉人追求“长寿、高效、节能、环保”,特别对高炉内部的可视化和高炉料面/料层的检测情有独钟,进行了长期艰苦的探索。我们利用微波技术在高炉料面/料层的检测方面进行了近20年的研究和实践,并且得到了科技部863课题和国家自然科学基金委重点项目的支持。
我们的“面向指标优化的高炉布料过程建模与控制”项目以布料过程料面形状精准控制为手段,以高炉顺行和生产指标优化为目标,针对料面的形状和料层分布测量技术、料面形状的模型构建和特征提取方法、料面形状特征和煤气流分布以及炉况的关联关系、从料仓到料面的料流运动模型构建、基于生产指标优化的最优料面设定、料面形状的精准控制等进行了系统和深入的研究,取得了一系列创新成果。
一、 面向指标优化的高炉布料过程建模与控制体系
指标优化主要是根据当前炉况和料面料层变化,提取料面特征,经过优化计算获得下一批布料的期望料面设定并生成布料矩阵;再通过对布料过程各各环节的料流运动模型,实现布料精准控制。
图1 面向指标优化的高炉布料过程建模与控制体系
项目的总体研究框架如图所示。
图2 总体研究框架
二、 多场相耦合的高炉料面形状与煤气流分布检测方法
1.高炉料面形状与料层分布检测
1)料面特征提取:
基于雷达检测技术以及布料机理模型,建立了高炉料面“1D-2D-3D”定义体系,并设计了相应的特征提取策略。高炉料面1D模型指的是高炉料面的单点检测,是高炉布料中,最为原始的获知料面形状的手段;高炉料面2D定义模型针对于高炉径向料线数据,设计了七维形状特征参数提取策略,建立了料线和特征的对应关联模型;高炉料面3D定义模型能够更加准确的重构高炉料面形状,设计了线形、环形、以及扇形定义方式。高炉料面定义体系能够准确提取表征料面的特征参数,为后续料面优化和布料操作提供支持。定义方法有如下几个优点:(1)操作简便。料面定义基于雷达检测技术,对于2D料线模型,采用的是阵列雷达数据和旋转扫描雷达数据,3D料面重构采用的是相控阵雷达数据。由于雷达检测技术的引入,使得高炉料面的重构和定义变得简单方便;(2)形状特征参数准确有效。在进行料面和料线特征提取之前,建立了料线和料面拟合模型,摆脱异常检测点对于模型的影响;(3)转换料面控制为参数控制问题。以特征变量表征料面形状,将料面控制问题转换为多参数控制问题,满足传统控制策略要求,推动布料自动化控制的发展。
图3 高炉料面2D线形定义
2)料层分布检测:
针对高炉料面检测应用,开展了高炉阵列雷达理论与方法的研究。首先基于高炉封闭空间复杂环境,研究矿物-煤气-焦炭的多元高温固体混杂共存的特殊介质电磁衰减特性,对混杂共存的特殊介质提出气固两相流的简化建模,对电磁波穿越强动力学环境下的电磁衰减和相位偏移方程引入修正参数,提出气固两相流的电磁衰减模型;然后研究粉尘、水雾、火焰等具有复杂空间结构和分形特征的复杂介质对高炉阵列雷达应用的影响,提出高炉复杂环境下的信号建模、特征提取和参数修正方法;最后基于阵列流型理论,将高炉炉顶阵列优化布设抽象为在限制子空间中阵列流型向量的求解优化过程,并对空间位置受限的阵列优化进行了仿真研究。
针对高炉料面形状模型的准确度问题,提出了基于多源数据融合的料面形状建模方法。首先针对高炉上相互独立的异类传感器造成整体数据采集系统的一致性欠、完备性差问题,提出基于混沌捕鱼策略的异类传感器优化布置方法;然后基于力学机理、布料机理、料线知识和单源数据(雷达高度数据、温度数据)建立料线形状模型,提出基于Bayes估计的料线形状多源融合建模方法;并考虑料面形状偏心性问题,进一步提出基于Co-Universal Kriging估计的高炉料面形状多源数据融合建模方法;最后考虑机理预测模型具有不确定性、准确度较低等问题,提出基于捕鱼策略的极限学习机建立高炉料面形状预测模型的方法,引入捕鱼策略优化基于结构风险与经验风险最小时的输入权值矩阵和隐含层偏差。该料面形状建模方法与传统料形估算法模型相比,其料线模型准确度提高了5.4%,同时预测模型在实测点处的预测平均误差达0.027%,比机理法降低了2.61%。
针对高炉内部复杂环境噪声情况下,运用新体制MIMO雷达改进传统的分布式阵列雷达和相控阵雷达。首先依据高炉天线单元的设计需求确定MIMO天线单元设计参数,利用CST软件仿真得到天线整体结构,围绕耐高温、高压、抗粉尘和小型宽带的设计要求设计了金属矩形波导介质填充天线,同时从阵列布阵优化角度提出 的T形MIMO阵列;其次分析9~11GHz各个频率段天线单元的波束宽度、增益以及旁瓣电平,提出改进的混沌遗传算法,利用新颖的二维Cat混沌映射和Tent映射,降低天线阵的最大相对副瓣电平;然后根据MIMO雷达成像原理,结合高炉内特定电磁环境的先验知识,建立一套适用于复杂工业环境的MIMO雷达成像模型。
2.高炉料面煤气流分布检测
针对煤气流发展分布过程,融合机理分析和数据驱动建模,基于现场运行的历史数据和实验数据、以及长期操作的专家经验,提出了煤气流动态分布及相关高炉状态的软测量和预测方法。
1)料面及煤气流三维热传递机理模型和测量模型
针对高炉炉喉煤气流分布无法直接检测的问题,通过已标定的摄像机检测煤气流形态, 并对检测图像进行预处理。通过Canny边缘检测算法提取二值图像的边缘特征点,并采用基于方向链码的边缘跟踪算法,得到煤气流形态的图像坐标。根据坐标系三维变化关系以及坐标映射关系,结合煤气流形态的图像坐标以及摄像机的内部参数,计算得到高炉炉喉煤气流形态在三维空间的坐标, 从而建立煤气流形态的三维模型。
2)料面形状、温度场的多源异类信息融合方法
针对高炉炉壁温度检测系统中由于传感器故障导致的检测信息不完备问题,提出一种基于多传感器数据融合的不完备检测信息软测量方法,从而有效的检测高炉边缘温度和煤气流发展状态。首先,依据高炉结构和炉壁温度传感器位置分布建立温度传感器位置描述模型和分区域温度检测模型;其次,根据热传递学分析炉壁分区域温度检测模型中各个传感器之间存在的相关性,并采用最大互信息非参统计量方法从传感器检测序列上定量的计算分区域温度检测模型中各传感器间的相关度;最后,依据相关性分析结果,结合温度传递规律,提出基于多传感器数据融合的炉壁温度检测不完备信息软测量模型,并采用Elman神经网络对模型的结构和参数进行辨识。
3)基于料面形状与温度场检测的料面煤气流分布动态估计方法
针对高炉煤气利用率发展过程常被误认为是随机过程的问题,提出了基于混沌学理论的高炉煤气利用率特性分析法方法,从定性、定量两个层面辨识高炉煤气利用率发展过程中的混沌特性,并采用改进支持向量机算法对煤气利用率实时预测。首先,基于相空间技术对时序样本进行空间重构。其次,通过C-C算法和G-P算法获取重构相空间中混沌吸引子的饱和关联维数,定性地证明高炉煤气利用率具有混沌特性。再次,利用自相关函数法获取重构相空间的时滞时间,根据关联积分法计算了两座高炉的Kolmogorow熵数值,定量地证明高炉煤气利用率发展过程具有混沌特性。最后,基于改进支持向量机方法建立了高炉煤气利用率预测模型,实现了煤气利用率的实时估计。
三、 高炉布料过程炉况状态建模方法
1.基于动力学原理的高炉布料过程炉料分布机理模型
根据实际高炉并罐式无钟炉顶设备参数,建立了并罐式无钟炉顶系统三维几何模型,利用离散单元法分别研究了炉料在上料过程、装料过程和布料过程中的运动行为及分布规律,分析了炉料在上料主皮带、料罐周向及径向和炉喉径向及周向上的分布及粒度偏析情况。
(1)针对串、并罐式无钟炉顶系统和不同型式布料溜槽布料差异性,在对布料过程中炉料颗粒受力状况分析基础上,建立节流阀出口处炉料流速数学模型、节流阀至溜槽间炉料下落运动数学模型、多环布料过程中半圆形截面溜槽和矩形截面溜槽内颗粒运动三维数学模型、空区内炉料运动三维数学模型、炉料落点及瞬时流量数学模型和料面形状数学模型等。
(2)利用建立的布料数学模型计算分析无钟炉顶型式、中心喉管内径、溜槽悬挂点高度、溜槽倾动距、溜槽长度、溜槽截面形状等主要无钟炉顶设备结构参数对布料过程炉料运动及分布的影响。
(3)利用建立的布料数学模型评估炉料种类、并罐式炉顶“倒罐”模式、节流阀开度、溜槽倾角、溜槽转速、溜槽转向、料线高度及煤气流速等高炉生产相关参数对布料过程的影响。
(4)对实际5500 m3并罐式无钟高炉整个装料过程进行仿真研究,分析左料罐装入焦炭和右料罐装入矿石时料罐内颗粒分布以及排料过程中颗粒分布规律,分析颗粒在中心喉管、旋转溜槽及空区内运动轨迹及分布,分别研究炉喉初始料面为“平面”和“平台—漏斗”状时炉料堆积轮廓及颗粒偏析分布。
2.高炉布料过程炉况状态动态模型
在考虑高炉冶炼过程的滞后性,以及高炉长期保持稳定顺行的前提下,提出了对煤气流分布进行预测,通过预测结果与当前炉况最优煤气流分布的比较来确定布料决策,从而降低能耗。预测部分,定义预测周期为布料周期,采用最小二乘支持向量机(LS-SVM)多步预测方法预计下一次布料前高炉料面温度场与煤气流分布模式。寻找最优煤气流分布模式部分,结合对温度场灰度向量的K-Means聚类算法,将较优煤气利用率下的灰度数据进行聚类,得到较优的分布模式。最后,将预测得到的煤气流分布模式归类到某种较优分布模式下,通过比较来确定下一阶段的布料决策。
针对高炉内部煤气流分布在线检测困难的问题,利用高炉炉况数据信息对高炉煤气流分布的影响,提出了对煤气流分布进行预测,通过对高炉煤气流分布模式的预测,为布料提供参考,从而达到优化高炉操作,提高经济效益的目的。结合高炉料面温度场及具有遗忘因子的在线序列学习算法即WOS-ELM,提出了一种基于高炉料面温度场煤气流分布的预测模型。最后,将预测得到的煤气流温度值建立料面温度场,来确定下一阶段高炉的布料决策。
基于武汉钢铁集团高炉现场真实工业数据,提出了基于在线序列超限学习机(Online Sequential Extreme Learning Machine,OS-ELM)的高炉煤气流分布的预测方法;分析了炉况各指标与煤气流温度的关联关系,建立了炉况指标与煤气流温度的关系模型。建立煤气流分布单步预测模型。基于单步预测模型,采用向量迭代的方法,进一步建立煤气流分布多步预测模型。提出了炉况指标与煤气流温度建模方法。对炉况各指标进行关联性分析,确定炉况参数,采用多输出支持向量回归(Multi-output Support Vector Regression,M-SVR)算法建立高炉炉况指标与煤气流温度的多输入多输出非线性模型。
3.高炉生产指标、炉料分布子模型与高炉炉况状态之间的关系模型
针对目前煤气利用率预测模型的研究缺陷,基于高炉数据的特点,提出了改进的超限学习机的煤气利用率预测模型。为了确保模型的准确性,首先从高炉生产机理出发,并结合灰色关联分析方法,确定影响煤气利用率的关键因素;然后,对所选择的操作参数的数据进行预处理,以降低高炉现场复杂环境对建模的影响。最后,提出了一个改进的在线超限学习机算法实现煤气利用率的在线预测。
针对传统透气性指数测量模型的缺陷,考虑到高炉生产数据含有大量噪声,运用小波去噪方法消除数据的噪声干扰。然后建立高炉透气性指数预测模型。在建模过程中,将偏最小二乘(Partial least square, PLS)与多层超限学习机算法结合,消除多层超限学习机最后一层隐藏层的多重共线性,提高了模型预测精度。并且所提出的改进算法称为PLS-ML-ELM。最后使用现场生产数据对该模型训练和测试,预测结果表明所提出模型能够快速、精确地预测高炉透气性指数,并且为高炉的后续操作提供有效的决策与支持。
四、 基于炉况和指标的精准布料控制方法
1.基于炉况诊断评价的指标优化与炉况状态设定方法
针对高炉这一复杂的“黑箱”系统,首先根据高炉数据的特点,提出了基于改进的超限学习机的生产指标与状态参数之间的关系建模方法,从数据驱动的角度建立了煤气利用率的预测模型,基于现场采集的数据进行了仿真研究,预测结果表明所建立的模型能够快速、精确地预测高炉煤气利用率。同时,基于高炉生产宗旨和实践经验,从质量指标、能耗指标、顺行指标以及操作指标方面来考虑构建了一个可行的高炉生产指标体系,为后续指标优化提供帮助。在分析了高炉炼铁过程的特点和生产指标体系的基础上,根据高炉的运行宗旨确定优化指标,以高炉稳态顺行为操作目标,将指标量化后,将面向指标的料面优化总结为优化问题,建立了料面优化模型,采用生产指标与料面参数的关系模型,并采用优化算法进行寻优,获得适合当前炉况下,并使性能指标最优的高炉料面参数。模型充分考虑了下部调节参数对于性能指标的影响,使得模型更加准确有效,初步实现高炉布料过程控制的重要参考,为最终实现精准控制和自动化提供最优料面设定值。
2.高炉连续生产的精准布料间歇控制方法
1)布料间歇控制方法
高炉布料是高炉炼铁生产的重要调节手段,通过调整布料矩阵、布料时序和料制实现料面形状动态跟踪设定、料速稳定控制和炉型及气流的合理分布。
(1)面向性能指标的高炉精确布料控制体系架构
针对高炉布料过程,面向煤气利用率等性能指标综合优化,研究建立以布料过程炉况状态动态模型为核心的高炉精准布料控制体系架构。高炉布料参数与煤气利用率变化趋势关系模型。从机理的角度分析,布料参数的改变首先会引起高炉运行状态的改变,从而导致了煤气利用率的变化。实际生产中,操作人员对于煤气利用率变化趋势更加关心,煤气利用率的增加或者减少与高炉炉况由着密切的关系,而高炉炉况是由高炉状态变量的组合来表征。因此本项目从大量历史数据出发,以煤气利用率为优化目标,建立布料控制架构。
图4 面向煤气流利用率优化的精确布料控制架构
(2)面向精准布料的布料矩阵逆动力学模型求解方法
高炉布料的方式由布料矩阵决定,然而布料矩阵参数详细列出有几十个,并且在角度和原料重量上都会发生变化,假如全都作为输入参数进行模型训练,将会极大增加模型复杂度,降低模型性能。本研究通过机理分析并且结合现场实际,从布料矩阵对高炉状态的本质影响出发,将高炉布料矩阵参数特征加以整合,进行有效降维,将会极大减少建模时模型的复杂度以及信息冗余,提高模型训练效率以及收敛精度。
(3)面向高炉连续运行-间歇布料的炉况状态精确跟踪控制方法
在实现高炉布料操作控制的过程中,不仅需要分析高炉操作对状态指标等参数影响的时间尺度,也需要对高炉炉况进行分析。因为在高炉处于不同炉况时,即使是相同的布料操作方式,所得到的状态指标等参数的变化趋势也将是不同的,例如当高炉处于异常炉况时,就需要采取不同的布料策略。针对高炉过程数据存在大量不确定性和冲突信息的问题,本项目基于不确定性推理方法DS证据理论提出一种有效处理冲突信息的高炉故障诊断方法。
2)精准布料
传统布料矩阵通过设定溜槽倾角以及转动圈数,能够实现多环布料。此种布料措施较为粗糙,理论上在同一布料档位上,单位时间内的料流体积是均等的。精准布料操作需要改善均匀布料方式,计算布料档位不同位置需料体积,设置节流阀开度自调节和溜槽转速自调节的精准布料策略,实现炉料精准落点。
图3 精准布料流程图
建立精准布料控制理论体系,包括基于节流阀开度自调节和基于溜槽转速自调节的高炉精准布料策略。节流阀开度控制着炉料单位时间内的下降体积,通过建立节流阀开度与出料体积的关联模型,能够保证将合适体积的炉料布置在相应的布料单元上。溜槽转速控制了溜槽划过不同布料单元的时间,建立溜槽转速与布料单元需料体积关联模型,实现精准布料操作。节流阀开度自调节模型,旨在建立节流阀开度与布料单元需料体积自适应变化模型。溜槽转速自调节模型,旨在建立溜槽转速与布料单元需料体积自适应调整模型。高炉精准布料研究,改变了传统的粗糙布料策略,有助于推进高炉布料的自动化、精准化和智能化发展。
五、 高炉布料过程可视化实时仿真平台与布料过程优化控制工业应用系统
以华菱涟源钢铁股份有限公司 2800m3 高炉为应用对象,将本项目的研究成果在实际高炉生产过程中进行工业应用探讨。高炉现场过程计算机系统主要的任务是完成高炉炼铁生产过程中产生的数据进行收集、对模型进行计算和优化控制、过程监视、操作指导、生产数据的分析和管理、数据通信和报表打印等功能。高炉总体的自动化系统分为 3 级:L1 级为基础自动化级,其主要组成部分为现场 PLC、检测仪器仪表、执行结构及其操作站,主要负责炼铁过程的逻辑控制、回路控制、人机接口和数据通信;L2 级负责对冶炼生产过程中的的数据进行收集、对模型进行计算和优化控制、过程监视、操作指导、生产数据分析和管理、数据通信和报表打印等功能。L3 级生产管理计算机系统主要通过焦化厂、烧结厂和炼铁厂之间的数据通信和协调,从而确保高炉的正常冶炼生产。现场调试主要是在高炉监控室完成。高炉煤气流三维成像以及布料制度设定软件主要完成以下功能:对现场实际生产过程进行监视,采集高炉生产过程实时重要数据,完成炉喉温度检测及成像、顶温/炉壁温度/透指的预测、矿焦比实时计算、布料参数设定、煤气利用率趋势的预测。
图4 高炉生产过程组态监视画面
图5 高炉径向方向煤气流分布成像
图6 布料制度决策软件运行画面